Industrie 4.0 : Kontaktsport
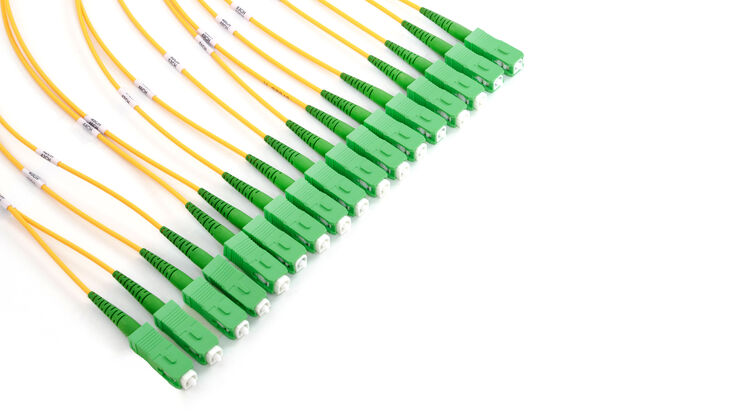
Wilfried Sihn ist alles andere als ein Pessimist. Das passt nicht zu seinem Naturell – und verträgt sich zudem schlecht mit seinem Job. So bleibt der Produktionsforscher, der in großen Maßstäben und Effizienzkategorien denkt – ziemlich cool, wenn er an die Eröffnung der Pilotfabrik für Industrie 4.0 denkt: Gern hätte der Leiter des Fraunhofer-Geschäftsbereichs Produktions- und Logistikmanagement diese schon zu Jahresbeginn abgehakt. Doch so schnell geht es jetzt nicht: Eine Eröffnung frühestens im Sommer ist avisiert. Ärgerlich, aber nichts, womit Sihn nicht umzugehen weiß. Was ihn dagegen wirklich auf die Palme bringt: Die mangelnde Bereitschaft einiger Hersteller, die Offenheit der Produktion durch vereinheitlichte Schnittstellen mitzutragen. Dies könne das Projekt Industrie 4.0 ernsthaft gefährden, sagt Sihn. Zwar sei es grundsätzlich richtig, dass deutsche Hersteller und Verbände in ihrer Normungsroadmap Industrie 4.0 gemeinsame Standards für die Zukunft schaffen wollen – wirklich honorieren kann Sihn dieses Vorhaben aber nicht. Der Grund: Das Vorhaben sei von Firmen getrieben, die versuchen, ihre eigenen Schnittstellen durchzusetzen: Hersteller seien sich "alles andere als grün", ein "Machtkampf hinter verschlossenen Türen findet derzeit statt", kritisiert Sihn.
Abschottung statt Offenheit
Die trotzige Einschätzung eines Mannes, dem es nicht schnell genug gehen kann? Bloße Provokation? Wohl kaum. Zwar beteuern Hersteller, auf mittlerweile größtmögliche Offenheit zu setzen – so etwa preschten die Roboterbauer früh vor. "Dank Ethernet-Schnittstelle ist unser Roboter für alle zugänglich", betont der Geschäftsführer einer österreichischen Niederlassung, das Thema Herstellerneutralität hochzuhalten. Informationen über den Systemzustand des Geräts seien keine Geheimwissenschaft – man verberge "nichts". Auch die großen Feldbusschlachten – ausgetragen unter namhaften Anbietern von Industrieelektronik – liegen schon Jahre zurück. Und trotzdem ist die Gemengelage vielerorts immer noch die selbe: Hersteller schotten ihre Technologie ab. Keiner will dem Mitbewerb den Markt – etwa für ganze Automatisierungssysteme von der Steuerung bis ins Feld – überlassen. "Es besteht mitunter bestenfalls geheucheltes Interesse, offene Lösungen anzubieten", sagt ein Automatisierungsprofi. Ein großer Industrieautomatisierer blockierte jahrelang die Normierung seiner Funktechnologie – man entzog sie erfolgreich dem neugierigen Mitbewerb, Anwender hatten weniger gut lachen. Eine Normung wäre für uns "ein Problem", gibt ein Geschäftsführer eines ebenfalls auf Funkautomation spezialisierten Betriebs unumwunden zu. Sein Betrieb lizenziert Fremdsysteme und verdient gutes Geld damit. Ein Umsatz, der ihm zwischen den Fingern zerrinnt, würde eine Norm Mitbewerbern "alle technologischen Details offenlegen", sagt er. So denken viele – die Vorkämpfer der Gemeinschaftsbewegung Industrie 4.0 bringt das in höchste Nöte.
1. Januskopf Normierung
In der Normungsroadmap Industrie 4.0 demonstrieren Hersteller Geschlossenheit. Doch das täuscht: Alleingänge, die das Großprojekt Industrie 4.0 gefährden, sind zu erwarten.
Sie steht in den Startlöchern: Im Herbst soll die zweite Fassung der deutschen Normungsroadmap Industrie 4.0 kommen. "Nach dem Grundsatzpapier kommt jetzt die Vertiefung durch Anwenderfälle", gibt ein Arbeitskreis-Mitglied des Fachbereichs 9 der DKE zu Protokoll. Letztere seien – neben weiteren Punkten wie der Veröffentlichung eines sogenannten Referenzarchitekturmodells – für die Vereinheitlichung von Standards entscheidend. Dass große Hersteller – im Arbeitskreis vertreten sind Siemens, ABB, Harting oder Phoenix Contact – die Diskussionen in eine für sie vorteilhafte Richtung drängen würden, mag der Mann nicht bemerkt haben. "Wir arbeiten konsensbasiert", sagt er. Über ebenfalls im Arbeitskreis vertretende Verbände seien zudem zahlreiche Interessensvertreter von KMU an Bord – ein nützliches Korrektiv. Allerdings räumt er ein, dass die Mitarbeit von Großkonzernen schon Gewicht habe. "Aber hier wird nicht diktiert und alle hüpfen nach", betont er. Schlussendlich werde man bei vielleicht 250 bis 300 Normen landen, es werde weg vom Produkt hin zum System gehen. Ob er mit Widerständen rechnet? Ausschließen mag er nichts. Soll heißen: Die Reduzierung der Normen könne für Anwender nützlich, für Hersteller zum Problem werden. Letztere könnten sich quer legen – wie sie es schon mehrfach getan haben: Werkzeuge mit unzähligen Schnittstellenprotokollen hätten zu "schwindender Transparenz" geführt, zu "Problemen bei der Stabilität der Gesamtsysteme", fasst die Normungsroadmap die Fehlentwicklungen der letzten Jahre nüchtern zusammen. Die Chance, dass es wieder passiert, ist groß. Dann würde das "wohl wieder der Markt regulieren", glaubt ein Experte des Fachbereichs 9. Und das wäre dem jetzigen Szenario sehr ähnlich: "Käufer von Automatisierungstechnik würden sich sehr genau anschauen müssen, welche Erzeuger herstelleroffen denken und welche glauben, ihren Kopf durchsetzen zu müssen".
2. Theorie sticht Praxis
2020 soll eine Software die Protokolle Profibus, Fieldbus und Hart besser adressierbar machen. Doch wie ernst es die Hersteller meinen, ist fraglich.
Der Leitspruch der Systemhersteller ist leicht zu merken: Sei besser als die Konkurrenz. Das gehört zum kleinen Einmaleins der großen Industrieelektroniker, weiß auch der Experte des deutschen Messgeräteherstellers, der lieber ungenannt bleiben will. Die Folge: In der Automatisierungswelt über Jahrzehnte ausgefochtene blutige Kämpfe. Schlag nach bei der Verfahrenstechnik: Hier halten sich mit Profibus, Fieldbus und Hart gleich drei Protokolle am Leben. Für Komponentenhersteller ein Mehraufwand: "Wir bringen Artikel wie Drucktransmitter mit drei verschiedenen Anschlüssen auf den Markt", erzählt der Mann. Zusätzlich müsste im Sensor auch noch für alle drei Typen eigens angepasste Software sitzen. "Darüber hinaus gibt es noch einmal sieben oder acht gängige Systeme, die auf den drei Standards aufsetzen und eine Spezifika mitbringen", erzählt er. Für den Messgerätehersteller heißt das vor allem eins: testen, testen, testen. Für den Anwender ist dieser Wildwuchs um nichts angenehmer: Fällt ein Gerät aus, muss er um einen hohen Preis ein Ersatzgerät besorgen, das je nach Protokolltyp nach seinen ganz eigenen Spielregeln integriert werden will", schildert der Experte. Immerhin: Ein Teil des Problems dürfte bald der Vergangenheit angehören. Eine US-Organisation namens FDI, die sich die einfachere Feldgeräte-Integration auf die Fahnen geschrieben und so prominente Hersteller wie ABB, Honeywell und Siemens an Bord hat, steht dieser Tage vor dem Durchbruch: "Eine Spezifikation ist fertig gestellt", heißt es in der Branche erleichtert. Eine Software (EEDI) soll künftig als Übersetzungshilfe der drei Protokolle Profibus, Fieldbus und Hart dienen – der Prüfaufwand für Komponentenfertiger zugleich sinken und Herstellerunabhängigkeit endlich Realität werden. Theoretisch. Denn in der Praxis ist noch lange nicht beschlossene Sache, dass die Hersteller derart offene Systeme auch wirklich zulassen. Denn die Bereitschaft der Hersteller, die nunmehr entwickelten Übersetzungs-Softwarebausteine auch tatsächlich in ihre Systeme aufzunehmen, ist einem Experten zufolge enden wollend. "Ich will den Teufel nicht an die Wand malen", sagt er, "aber wie ernst es die Systemhersteller wirklich meinen, bleibt abzuwarten." Ohnehin sei FDI im besten Falle frühestens in fünf Jahren in den Systemen umgesetzt. Sie sei jedenfalls "explizit ein Fall für Industrie 4.0", heißt es in der Branche. Ein Lippenbekenntnis wäre fatal.
3. Giftküche F&E
Immer wieder höhlen Hersteller durch Spezialentwicklungen Standards aus – der Kunde zahlt drauf
Es erinnert ihn an den durchaus blutig geführten Videorekorder-Formatkrieg Ende der Siebziger: VHS, Betamax und Video 2000 ritterten um die Vorherrschaft in den Wohnzimmern. Gleiches passiere seit Jahrzehnten in der Automatisierungswelt, sagt der Entwickler eines deutschen Verbindungstechnikherstellers – und nennt als Beispiel das Ethernet-Protokoll. "Es gab eine viel größere Anzahl an Derivaten, als Sie dazu im Markt heute finden", erzählt er. Normen helfen manchmal, aber längst nicht immer, die Alleingänge der Entwickler zu entschärfen: Die IEC61131 – befasst mit den Grundlagen speicherprogrammierbarer Steuerungen – sei dafür ein gutes Beispiel, sagt der Experte. Zwar folge man der Norm, das sei nicht das Problem. "Trotzdem versuchen Steuerungshersteller einen gewissen Mehrwert, der über den Standard hinausgeht, ins System zu bringen". Die Kompatibilität wird so erst recht wieder untergraben. Für Kunden birgt das ein nicht unwesentliches Risiko, wie der Experte nüchtern festhält: "Er läuft Gefahr, in die falsche Technologie zu investieren." Ein ähnliches Szenario sei auch in der vollvernetzten Fabrik nicht denkunmöglich. "Man wird sich auf ein gewisses Level der Standardisierung einigen, aber darüber hinaus werden Hersteller mit Spezialansätzen vorpreschen", glaubt er. Wirkliche Flexibilität – ein Grundpfeiler der Industrie 4.0 – liefert eine solche Produktion dann nicht. Schon heute müssten etwa Anlagenbauer großen Programmieraufwand treiben, um Maschinenmodule unterschiedlicher Hersteller – also mit unterschiedlichen Protokollen als DNA – zusammenzuführen. "Wer aufs falsche Pferd gesetzt hat, muss schlimmstenfalls eine ganze Technologie tauschen".
4. Industrieller Bauchladen
Das Rennen um den besten industriellen WLAN-Standard hat gerade erst begonnen. Statt weniger Standards kommen die nächsten Jahre mehr – eine gefährliche Gratwanderung.
Mehrere industrielle Funk-Standards, und keiner ist perfekt, denkt Uwe Meier, Vorstand des Instituts für Industrielle Informationstechnik an der Hochschule Ostwestfalen-Lippe an die industrielle Funkautomation; sieht er deutliches Verbesserungspotenzial. Zu große Latenzzeiten, fehlendes automatisches Netz- und Sicherheitsmanagement, zu geringe Zuverlässigkeit: So fasst er die Schwächen derzeitiger Standards zusammen. "Ein neuer Standard soll die Probleme, mit denen Produktionsbetriebe seit Jahren kämpfen, nun lösen", sagt er. Ein sechseinhalb Millionen Euro schweres Projekt (Laufzeit: bis 2018) soll das neue System namens HiFlecs vorantreiben und Funksysteme schneller und zuverlässiger machen. "Sie können heute schon Daten per Funk an einen Roboter übertragen, aber wir gehen davon aus, dass es mit HiFlecs noch deutlich besser geht", sagt Meier. Ein ideales Szenario für Industrie 4.0, wo alles mit allem kommunizieren soll? Ja und nein. Zwar könnte ein neues Protokoll plangemäß bisherige ersetzen. Doch trotz eindrucksvoller Industriebeteiligung – an Bord des Projekts unter Projektleitung der Universität Bremen sind unter anderem Hersteller wie Phoenix Contact, Siemens und NXP – kann man nicht von einem geschlossenen Vorgehen der Automatisierungsbranche sprechen – im Gegenteil. Denn Projekte, die den Schnittstellensektor konsolidieren sollen, gibt es zurzeit mehrere. "Wir haben eine Wettbewerbssituation, der beste neue Standard wird sich hoffentlich durchsetzen", räumt Meier ein. Dass es so auf absehbare Zeit erst recht wieder mehr Lösungsvielfalt gibt, irritiert ihn nicht. Meier: "Vielleicht verschmelzen die neuen Standards später dann zu einem."